The 10-Minute Rule for Alcast Company
Table of ContentsIndicators on Alcast Company You Need To KnowThe Facts About Alcast Company Uncovered3 Easy Facts About Alcast Company DescribedThe Of Alcast CompanyThe Alcast Company DiariesFascination About Alcast Company
Chemical Comparison of Cast Light weight aluminum Alloys Silicon advertises castability by reducing the alloy's melting temperature level and boosting fluidity throughout spreading. Furthermore, silicon adds to the alloy's strength and put on resistance, making it beneficial in applications where sturdiness is vital, such as vehicle components and engine parts.It likewise improves the machinability of the alloy, making it easier to process right into completed products. By doing this, iron contributes to the general workability of aluminum alloys. Copper boosts electrical conductivity, making it useful in electric applications. It also enhances rust resistance and includes in the alloy's total toughness.
Manganese adds to the stamina of aluminum alloys and enhances workability (Casting Foundry). It is typically used in wrought aluminum items like sheets, extrusions, and accounts. The existence of manganese help in the alloy's formability and resistance to fracturing throughout manufacture procedures. Magnesium is a light-weight element that gives strength and impact resistance to light weight aluminum alloys.
Getting The Alcast Company To Work
It enables the manufacturing of lightweight parts with superb mechanical residential or commercial properties. Zinc improves the castability of light weight aluminum alloys and helps control the solidification procedure throughout spreading. It improves the alloy's toughness and firmness. It is commonly discovered in applications where complex forms and fine details are required, such as attractive spreadings and specific automobile parts.
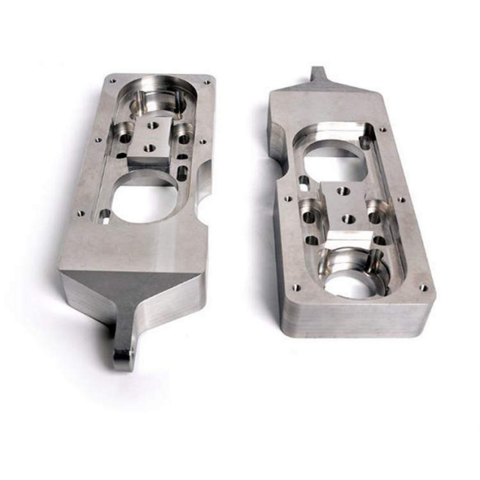
The key thermal conductivity, tensile stamina, return stamina, and prolongation vary. Select appropriate basic materials according to the performance of the target item created. Amongst the above alloys, A356 has the highest possible thermal conductivity, and A380 and ADC12 have the most affordable. The tensile restriction is the contrary. A360 has the best yield strength and the highest elongation rate.
6 Easy Facts About Alcast Company Explained
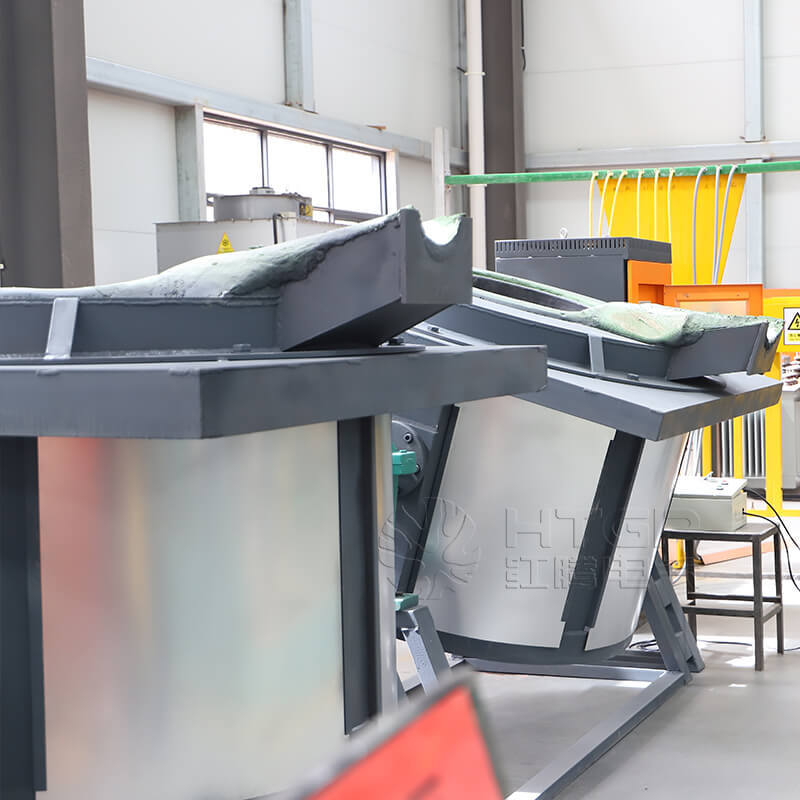
In precision casting, 6063 is well-suited for applications where detailed geometries and top quality surface area finishes are critical. Instances consist of telecommunication units, where the alloy's superior formability permits for smooth and visually pleasing styles while preserving architectural honesty. Likewise, in the Illumination Solutions market, precision-cast 6063 parts develop classy and effective lights components that call for elaborate forms and excellent thermal efficiency.
The A360 displays superior prolongation, making it perfect for complex and thin-walled components. In accuracy casting applications, A360 is well-suited for industries such as Consumer Electronics, Telecommunication, and Power Devices.
What Does Alcast Company Do?
Its distinct residential properties make A360 an important option for precision casting in these markets, boosting product longevity and high quality. Aluminum Castings. Aluminum alloy 380, or A380, is an extensively used spreading alloy with numerous distinct features.
In accuracy casting, aluminum 413 radiates in the Consumer Electronics and Power Equipment industries. This alloy's remarkable corrosion resistance makes it an exceptional choice for outside applications, guaranteeing long-lasting, long lasting items in the mentioned industries.
Not known Facts About Alcast Company
The aluminum alloy you select will considerably impact both the spreading process and the residential properties of the final product. Due to the fact that of this, you must make your choice very carefully and take an informed method.
Establishing the most suitable aluminum alloy for your application will certainly mean evaluating a vast array of characteristics. The very first classification addresses alloy features that impact the manufacturing procedure.
Our Alcast Company PDFs
The alloy you select for die casting straight impacts numerous aspects of the spreading procedure, you can check here like just how easy the alloy is to collaborate with and if it is vulnerable to casting flaws. Warm cracking, likewise referred to as solidification splitting, is a normal die casting flaw for aluminum alloys that can result in internal or surface-level tears or splits.
Specific aluminum alloys are a lot more prone to hot cracking than others, and your selection must consider this. It can harm both the cast and the die, so you should look for alloys with high anti-soldering homes.
Corrosion resistance, which is currently a remarkable characteristic of light weight aluminum, can differ significantly from alloy to alloy and is a vital particular to consider relying on the environmental conditions your product will certainly be exposed to (Casting Foundry). Wear resistance is one more home generally sought in aluminum products and can separate some alloys